Optical Polishing Services
What is Polishing?
Polishing is a process that uses abrasive materials to remove surface irregularities and create a smooth, reflective finish on a product. By choosing the right abrasives and polishing method, we can achieve finishes with precision down to the micron (μm) level, making this a critical final step for products requiring high accuracy.
At YISHUN Optical, we handle a variety of materials, including metals, ceramics, optical glass, and plastics, to provide precise polishing solutions for industries like electronics, optics, and aerospace.
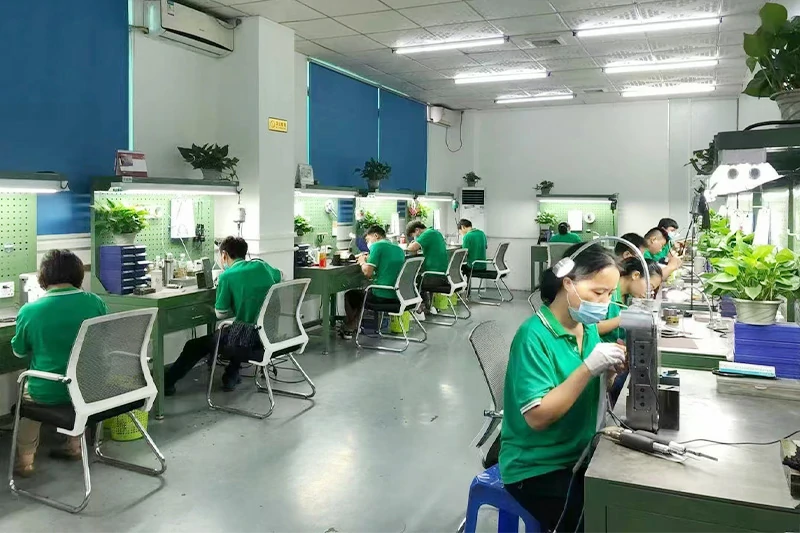
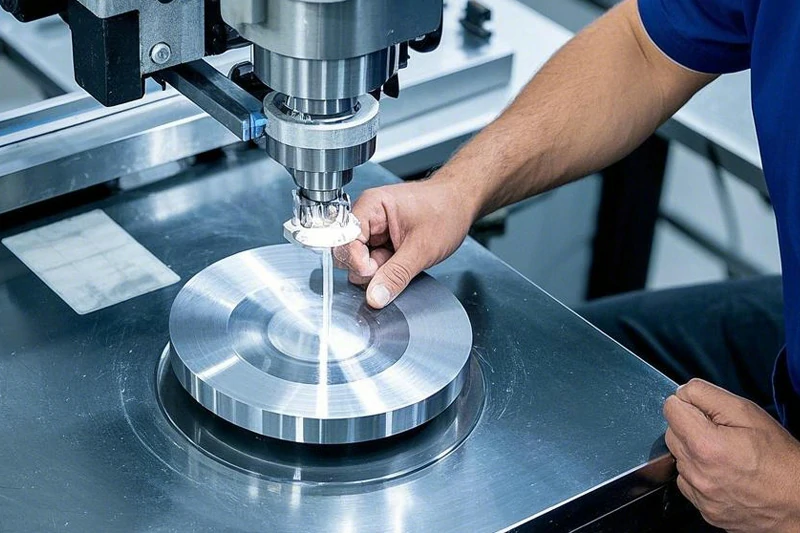
What’s the Difference Between Polishing and Grinding?
Both polishing and grinding are methods used to refine surfaces, but they differ in technique and outcome. Grinding uses a rotating wheel with coarse abrasives to remove material and shape the product. Polishing, on the other hand, involves fine abrasives (slurry) that remove very little material but create a smooth, high-precision finish with less stress on the material.
In many cases, both grinding and polishing are used in sequence to achieve the required surface accuracy.
Various Polishing Methods
We offer several types of polishing methods based on your needs
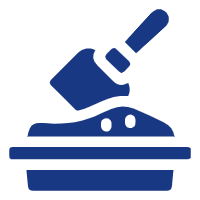
Lapping
Lapping involves two surfaces rubbing against each other with abrasive material in between. This technique is often used for achieving extreme flatness and is ideal for applications such as lens manufacturing, mold finishing, and optical component processing.
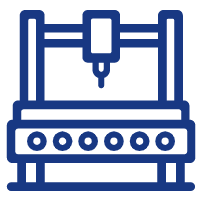
Polishing
Polishing uses soft materials like felt or cotton pads with fine abrasives to create a mirror-like finish. It’s typically used for the final surface finish, enhancing the smoothness and gloss of the material.
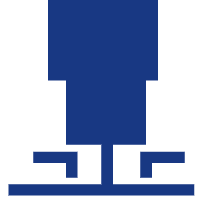
Grinding
Grinding is a rougher process where a grinding wheel is used to shape and refine the material. While it’s a primary method for shaping, grinding also prepares the surface for the finer work done during polishing.
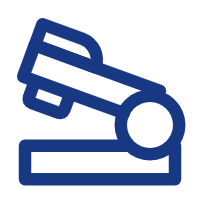
Barrel Polishing
Barrel polishing involves placing components in a rotating barrel with polishing agents. This method is ideal for mass polishing of smaller components and allows for consistent finishes in large batches.
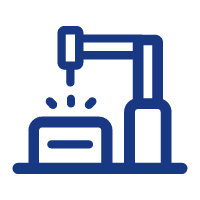
Cutting
Cutting is a rough machining process that shapes the material. After cutting, polishing is often done to refine the shape and finish.
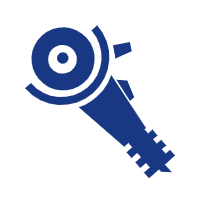
Coated Abrasives
Coated abrasives, such as sandpaper, are used for surface finishing in DIY, industrial, and production applications. This method uses a cloth or paper backing with evenly distributed abrasive grains.
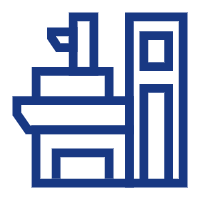
Electrical Discharge Machining
EDM uses electrical discharges to erode material. This non-contact process is ideal for machining hard materials and creating very precise shapes that are difficult to achieve with traditional methods.
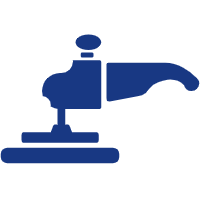
Electropolishing
Electropolishing is an electrochemical process where a product is immersed in a solution and polished using direct current. It’s effective for materials that are difficult to polish by traditional means, although it’s generally more expensive and limited to specific metals.
Types of Familiar Polishing Processes
In addition to industrial polishing techniques, there are simpler methods that are commonly used in daily life
Whetstone Polishing (Manual Work)
An example of manual polishing is using a whetstone to sharpen tools like knives. Though precision is typically not as high, it is a useful technique for everyday use.
Sandpaper Polishing
For DIY projects or light polishing, sandpaper is often used. It’s an accessible way to smooth surfaces or prepare them for further finishing.
Lens Polishing
In the production of camera and microscope lenses, manual polishing is often done in the final stages of manufacturing to ensure clarity and smoothness.
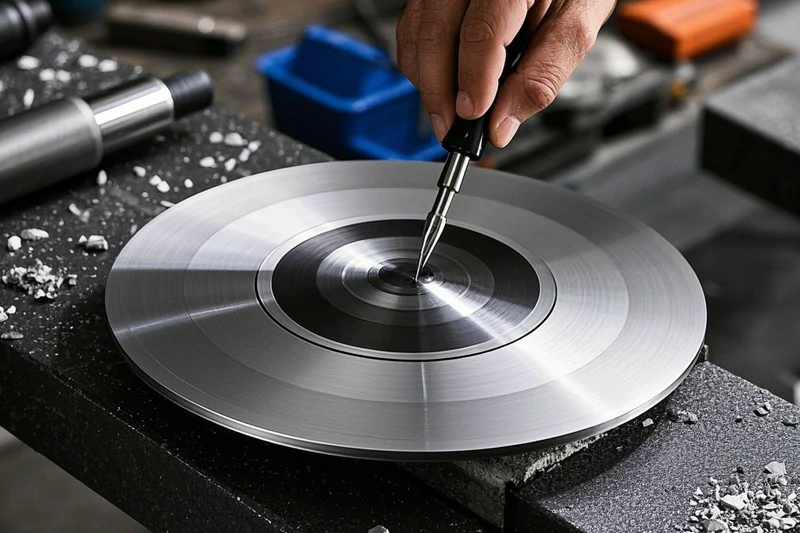
What are Abrasive Grains?
Abrasive grains are hard particles that act as “cutting tools” in the polishing process. They wear out during use and continue to refine the surface with each polish. There are two main types of abrasive grains: normal abrasives and superabrasives. Each type is suitable for different materials and applications.
Common abrasives include:
- Brown Alumina (A): Used for general steel and free grinding.
- White Alumina (WA): High-purity alumina, often used for hardened steels.
- Silicon Carbide (C): A harder abrasive, ideal for non-ferrous metals and cast iron.
- Green Silicon Carbide (GC): Used for high-precision materials like cemented carbide.
Polishing Procedure
Our polishing process is broken into several stages:
Rough Polishing: Coarse abrasives are used to remove large surface irregularities.
Medium Polishing: Finer abrasives smooth out the surface, removing smaller imperfections.
Finishing: The surface is polished with even finer abrasives to refine its smoothness and achieve the desired finish.
Mirror Finish: The final step involves using the finest abrasives to achieve a mirror-like surface with minimal material removal.
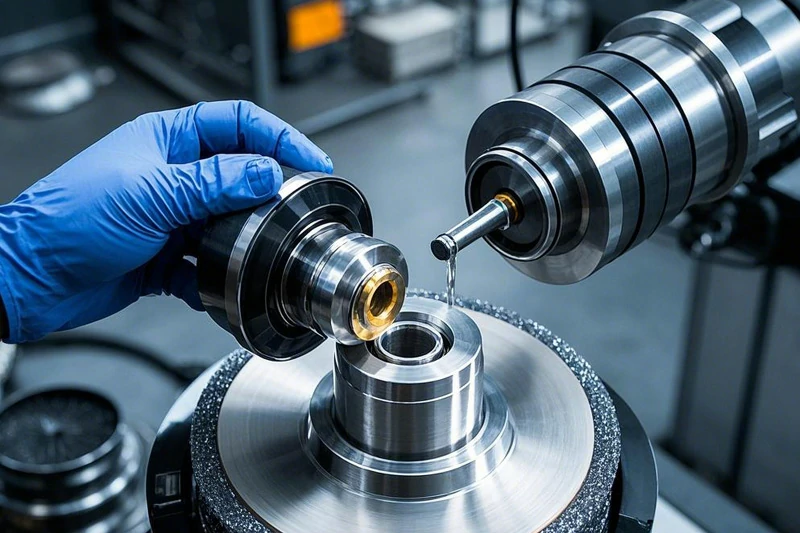
YISHUN Optical’s Polishing Technology
YISHUN Optical uses state-of-the-art equipment, including diamond lathes and high-speed CNC machines, to achieve precision polishing results. Our capabilities include surface roughness as low as Ra 1 nm and dimensional accuracy down to ±0.5 μm.
Materials We Process
Stainless Steel, Superalloys, Copper, Titanium, Aluminum, Tungsten, Nickel, and more.
Al2O3, ZrO2, SiC, Si3N4, Quartz, Sapphire, and more.
BK7, Si, SiC, Sapphire, and others.
PEEK, PMMA, and more.
Processing Achievement
Feature | Polishing | Lapping with GC |
Flatness | 0.1 μm | 1 μm |
Roughness (Ra) | 1 nm | Pear Skin Finish/Frost |
Parallelism | 1 μm | 2 μm |
Tolerance | ±0.5 μm | ±1 μm |
Why Choose YISHUN Optical?
With over 10 years of experience in precision optical and CNC machining, YISHUN Optical provides the highest quality polishing services with unmatched accuracy. Whether you’re working with metals, ceramics, or complex optical materials, we can deliver polished components that meet the most demanding specifications.
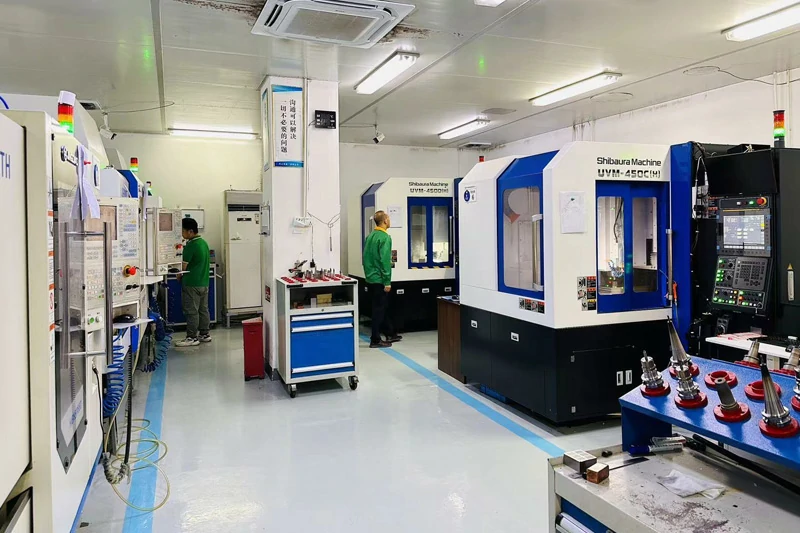
Applications
We process a wide range of components used in advanced industries
Wafer Chuck Plates & Precision Tables
We provide ultra-precision polishing for positioning plates and precision tables used in semiconductor manufacturing and precision measurement. Our services ensure high accuracy in flatness, parallelism, and dimensional tolerance.
Various Crystal Wafers
We perform precision Chemical Mechanical Polishing (CMP) and thin polishing of wafers made from materials such as silicon, sapphire, SiC, and diamond. We can handle small lots for experimental research or large-scale mass production.
Shims
Our shims are manufactured to guarantee high accuracy, with thickness variations as small as 1 μm. These are essential in applications requiring precise assembly, such as in electronic devices, medical equipment, and precision measurement tools.
Test Pieces
We process test pieces used in friction, wear, and tensile tests. Our service is versatile and supports rapid turnaround for experimental and testing purposes.
Surface Plates
Surface plates used for assembly and inspection require absolute flatness. We provide precision machining for both stone and ceramic surface plates, as well as thermal spraying for specialized surfaces.
Molds
We offer precision polishing for molds used in manufacturing products via injection molding, press working, and plastic working. Our expertise ensures that even complex shapes and lens molds are polished to the highest standards.
Spheres
Our polishing services extend to high-precision spherical components used in bearings, measuring probes, and other high-accuracy applications. We can achieve ultra-precision on spherical surfaces with strict tolerances for sphericity and roughness.
How Ultra-Precision Polishing and Machining Benefits Your Project
We’d like to hear about your projects and see how we can help.